Warehouse logistics is a critical component of any supply chain. When products aren’t moving from a supplier to a company or a company to a consumer, they are stored in warehouses. An optimized warehouse receives and despatches goods faster, reducing costs and boosting revenue. Businesses with optimized warehouse logistics, like Amazon, for example, enjoy a considerable competitive advantage.
What Does Warehouse Logistics Mean?
Investopedia defines logistics as “the overall process of managing how resources are acquired, stored, and transported.” In the most general sense, it is the management of the flow of things between the point of origin and the point of consumption to meet the requirements of customers or corporations. Warehouse logistics, therefore, has to do with the organized management of products entering and exiting a warehouse.
Warehouse Logistics Process
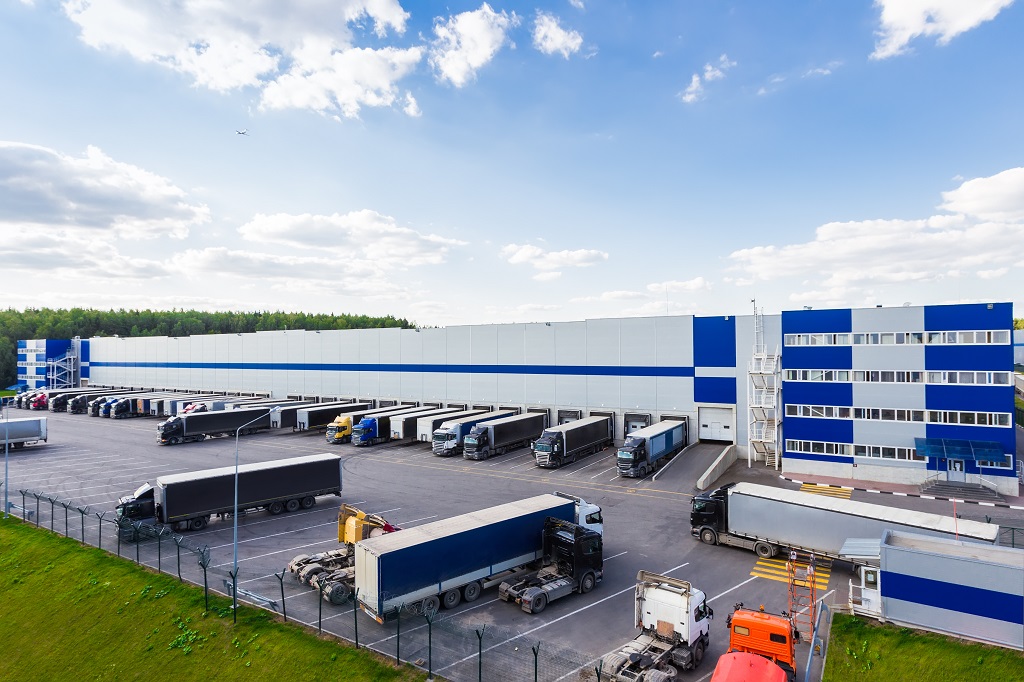
Six general processes take place in a warehouse; receiving, put away, storage, picking, packing, and shipping. A product received at a warehouse goes through quality control before it’s placed in a put-away bay and then transferred to an allocated storage location. When an order is received, the product is located and shipped to the consumer. If there’s no reserve stock to replace the product, a company places an order with its vendors to manufacture or send more.
What Is Better: Logistics or Supply Chain Management?
It’s incorrect to assume one is more superior than the other because they both serve different yet important functions. Let’s start by answering, “what is warehouse management in logistics?” Warehouse logistics involves the processes required to keep items moving in, around, and through a warehouse.
Logistics management is the process of integration and maintenance (flow and storage) of goods in an organization, whereas supply chain management is the collaboration between firms to connect suppliers and customers to boost value for the end consumer. The optimization of both processes improves customer satisfaction and business revenue.
Warehouse Logistics Benefits
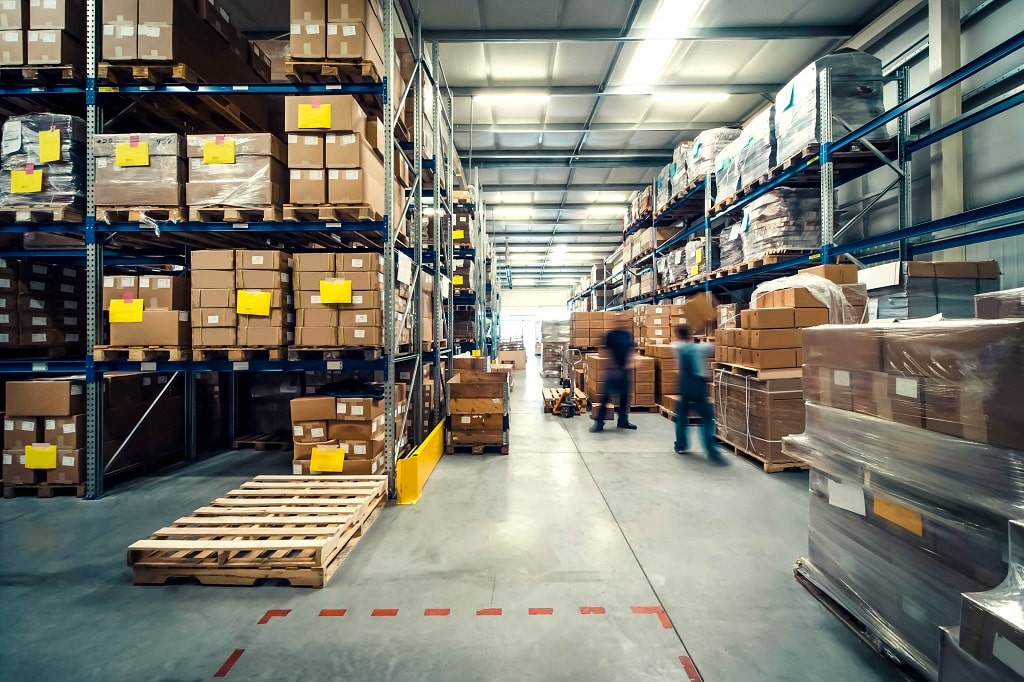
Increased revenue is the primary benefit of organized warehouse logistics, among others:
- Optimized storage space: Obtain the best inventory floor plan for location selection, inventory pick-up, and flow of goods.
- Effective labor: Companies can better assign the right task to the right staff member and at the right time.
- Improved Customer Service: Accurate inventory management means fewer returns and greater customer satisfaction.
- Inventory visibility: When companies have a better overview of their inventory, they can better plan which products to adjust for increased revenue or mitigate losses.
Logistics Management Challenges Faced by Warehouses
Every warehouse manager faces logistics challenges where they need to maximize performance while balancing trade-offs under fluctuating conditions. Supply chains are dynamic, so while the challenges can never be completely resolved, there are ways to improve processes to better manage obstacles as they arise.
- Poor facility layout: Inadequate storage and loading space can cause inventory mix-ups and traffic jams, wasting valuable time.
- Redundant processes: The unnecessary labor cost and time used when the same ticket passes through multiple hands.
- Inaccurate inventory: An inaccurate inventory count makes it difficult to maintain stock levels, accumulates obsolete inventory, and leads to inefficient processes.
- Seasonal Demands: Most companies have the data to predict seasonal demands, but occasionally, they may not possess enough stock to meet consumers’ orders or adequate space to store products.
- Handling returned items: The recent boom in eCommerce has left many businesses unprepared to deal with return surges.
How to Improve Your Warehouse Logistics
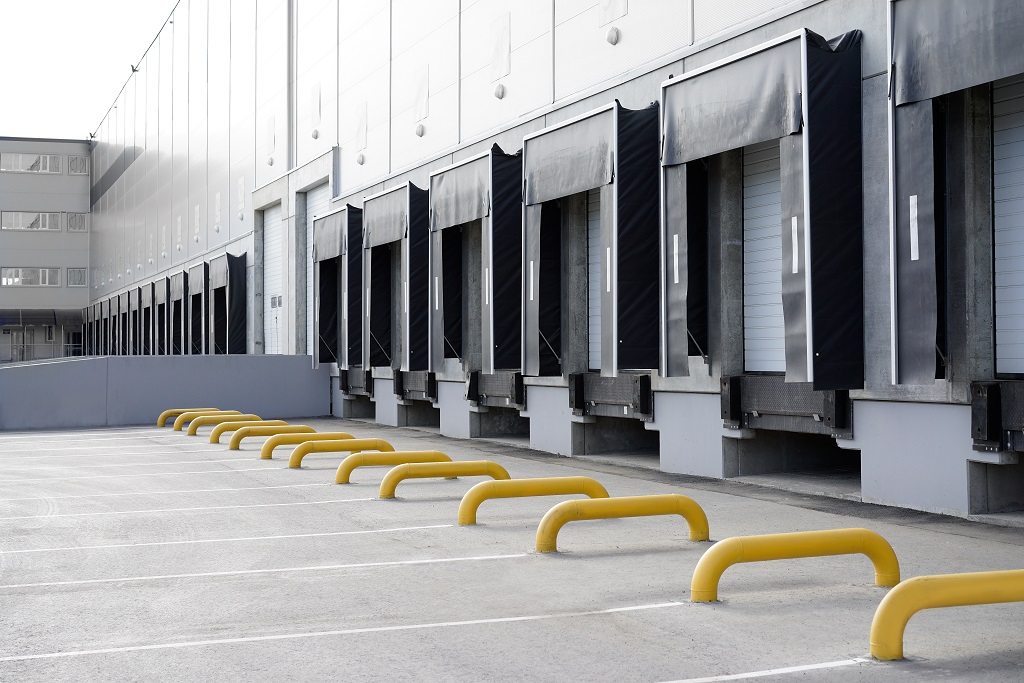
Meeting warehouse needs, employee requirements, and customer expectations remain a constant challenge for warehouse managers. Many companies use advanced warehouse management system (WMS) software to make the job easier because it provides visibility into a business’s entire inventory and manages supply chain fulfillment operations.
Identifying the most frequently picked products and rearranging storage locations to minimize distance traveled for picking these can help streamline floor movement. Additionally, using vertical space can also double the available storage volume. Investing in appropriate automation for data handling/inventory management standardizes processes and leads to optimal picking.
While the cost of warehouse maintenance is always at the forefront of company concerns, offering employee incentives can raise productivity. When employees know they’re appreciated and will be rewarded for effort, they’re more likely to improve throughput. Organizing workstations also goes a long way in boosting productivity. If staff members don't have to search for tools or equipment, they can do their jobs quicker.
Conclusion
There’s no one-size-fits-all solution for every warehouse challenge. To streamline operations, you require an agile team and management system that can weather shifts between supply and demand. Alternatively, you can also outsource your warehouse needs to a trusted third-party logistics provider like freight shipping company. We eliminate logistics management challenges faced by warehouses. Get a quote to find out about our effective warehousing solutions.